The Secrets of Automated Advanced Production Lines in Various Industries
- Share
- publisher
- guangzhou hongjiang
- Issue Time
- May 15,2018
Summary
The Secrets of Automated Advanced Production Lines in Various Industries
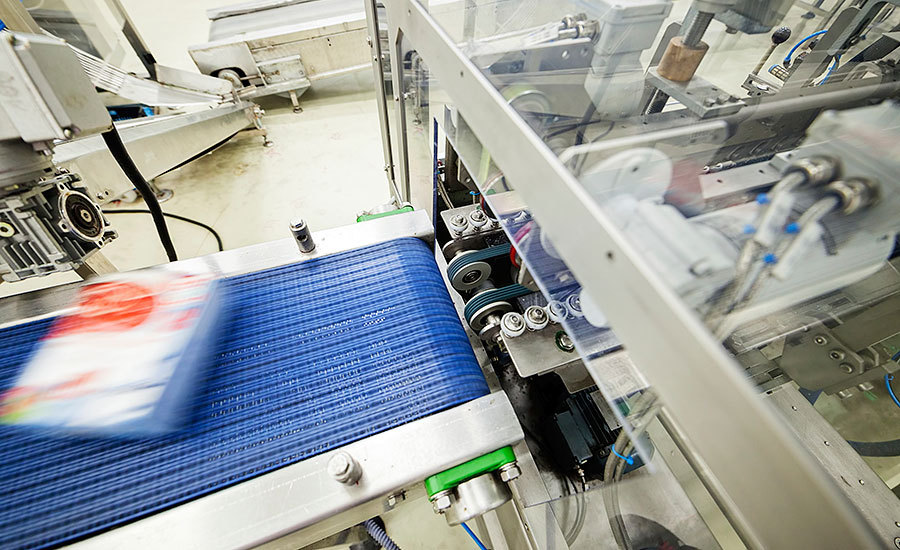
China’s demographic dividend has disappeared, and the labor costs of traditional manufacturing have become larger and larger, forcing companies to transform and upgrade their industrial structure. In order to better meet market demand, China's manufacturing industry must carry out automated production lines to increase production efficiency, reduce labor costs, and reduce dependence on a large number of labor forces. The popularization of industrial robots is an effective means to realize automated production, increase social production efficiency, and promote the development of enterprises and social productivity. At present, China's auto industry, electronic and electrical industries, construction machinery and other industries have begun automated advanced production lines, and more and more robots have entered different industrial fields.
It is only a matter of time before the popularity of manufacturing robots in our country. Since 2016, China has officially become the largest market for industrial robots in the world. In 2017, the sales volume of industrial robots in China exceeded 120,000 units, accounting for about one-third of the world's total production. It can be seen that in recent years, the development of industrial robots in China is very rapid. The following AGV manufacturer, Mick Lime, shares with you a few examples of the automation of the manufacturing line.
In 2008, Galanz introduced advanced automated production lines in new industries such as dishwashers and washing machines. Galanz's microwave oven automated production line is equipped with a robotic arm. The production cycle time is up to 15 seconds per station, the production efficiency is increased by 38% over the traditional production line, and the product pass rate is over 99%. Electric steamer automation assembly line, just 15 seconds, ordinary steel will become a complete electric steam oven cavity. This equipment line adopts advanced plasma and laser seamless welding. The entire electric steamer cavity automated production line requires only 3 technicians to operate, saving manpower resources by 72% and production speed by 16 times.
With the increasing production and sales volume, and rising labor costs, in order to enhance product competitiveness, guangzhou hongjiang company introduced 75 ABB robots in 2010 to carry out various aspects of production, such as mold opening, injection molding, and assembly. In the R & D plant, the electronic components of the plug, test, assembly, testing, packaging, palletizing of finished products are completed by industrial robots, AGV transfer robots instead of the material distribution and other personnel's labor. Pyramid has reduced the number of over 3,000 production workers to more than 800; in addition, the new product development cycle has increased from the original 3.8 months to 60 days, further solidifying the position of the domestic mouse and keyboard brand, and making it with international giants such as Logitech. There are more advantages in the competition.
In Dongguan, Huawei's fully automated production line of glory, the United States imported ultra-precision MPM dual-track printing presses, the world's leading Camelot dispensing dispenser, fully automatic arm control machine testing, automatic unmanned delivery trucks, AGV car As well as streamlined equipment consisting of six leading fully-automated robots being developed, it is an eye-opener. According to the person in charge of the plant's technology, it is currently developing the most advanced and unique automated line equipment in the world. It is a streamlined body composed of six fully automated manipulators. The device covers the load from the single board test and is fully automated. The functions of the workstations such as plate dispensing, audio testing of the whole machine, and software loading of the entire machine can greatly improve the consistency of the product quality and production efficiency. It is learned that a streamlined body can reduce the workforce by about 50 people, which can be described as extremely powerful.
Hongjiang company employs two 'tricks' to ensure high-precision manufacturing - laser on-line measurement and coordinate measuring instruments, and forging of high-quality bodywork. The two 'magic weapons' - ultra-high strength steel welding technology and lasers Brazing technology, using high-density automated welding robots and highly flexible GEO pallet conveyor lines, achieves the efficiency of producing a white body in less than a minute. With the AGV flexible production system, our company plant can achieve seamless production of different types of engines and transmissions on the same production line!
AGV is the most simple and effective automatic material transportation method in automated production line. It can realize the combination of overhead storage, operation and transportation of point-to-point automatic access, realizing the refinement, flexibility, and informationization of production and reducing the labor intensity. Improve logistics efficiency and quality, reduce logistics costs. Mikko Limei AGV provides flexible and efficient logistics transportation for the manufacturing industry. It can automatically avoid obstacles and self-finding routes during the automatic handling of the machine tool loading and unloading, automated production lines, automatic assembly lines, palletizing, and containers. Accurate, stable and efficient completion of intelligent transportation and automatic picking of goods.