What is material characteristics of PP, POM and PA
- Share
- Issue Time
- May 4,2018
PP POM PA material characteristics
1).POM polyoxymethylene
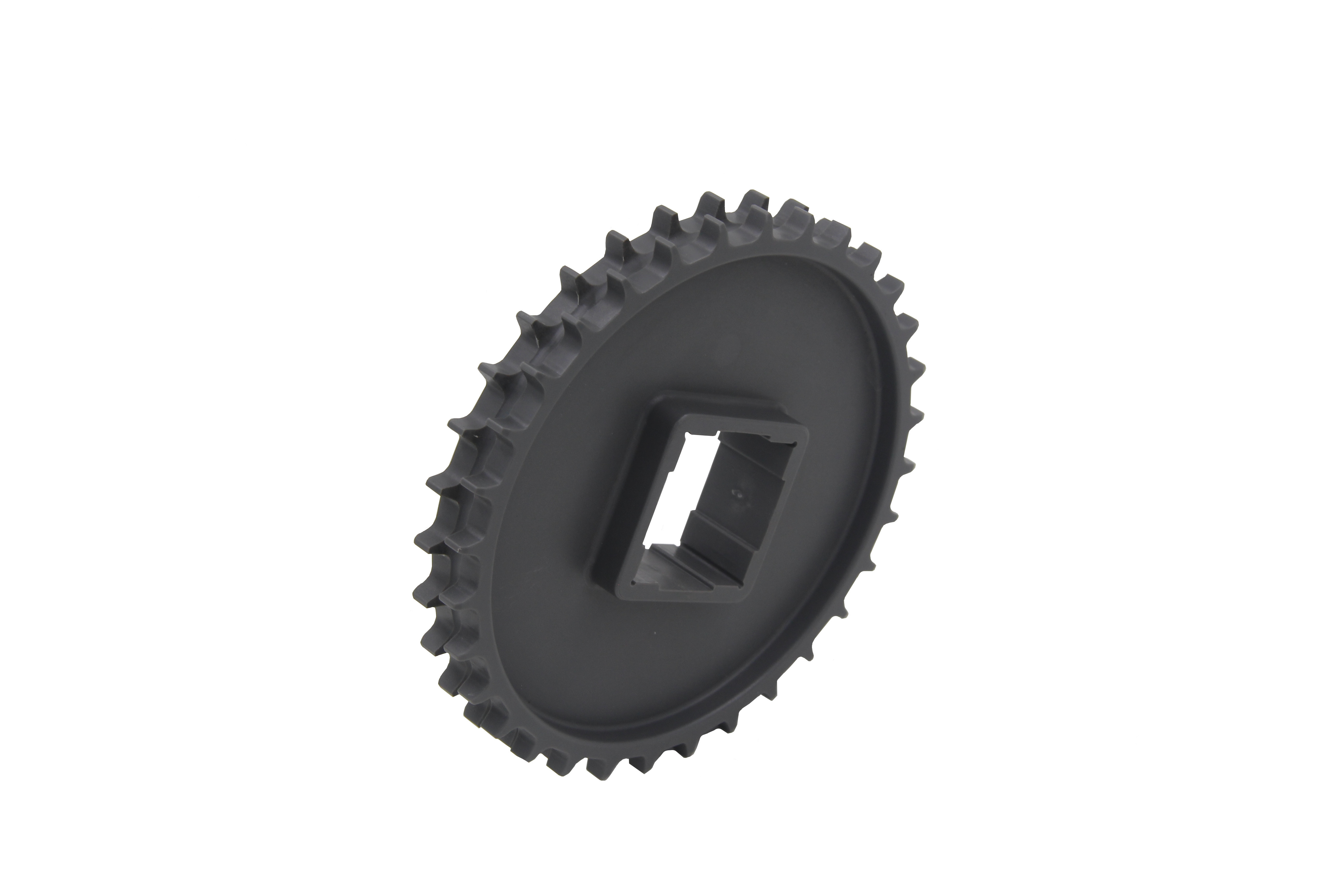
(POM material conveyor belt sprocket)
Typical Applications POM has a very low friction coefficient and good geometric stability and is particularly suitable for gears and bearings. Due to its high temperature resistance, it is also used in pipeline devices (valves, pump housings), lawn equipment, etc.
Injection Molding Process Conditions: Drying: If the material is stored in a dry environment, drying is usually not required. Melting temperature: The homopolymer material is 190-230°C; the copolymer material is 190-210°C. Mold temperature: 80 to 105°C. In order to reduce the shrinkage after molding, a higher mold temperature may be selected. Injection pressure: 700 to 1200 bar. Injection speed: Medium or high injection speed. Runners and gates: Any type of gate can be used. If tunnel-shaped gates are used, it is best to use shorter types. Hot-nozzle runners are recommended for homopolymer materials. For the copolymer material, either an internal hot runner or an external hot runner can be used.
Chemical and physical properties POM is a tough, elastic material that has excellent creep resistance, geometric stability, and impact resistance even at low temperatures. POM has both homopolymer and copolymer materials. Homopolymer materials have good ductility and fatigue strength but are not easy to process. Copolymer materials have good thermal stability, chemical stability, and ease of processing. Both homopolymer and copolymer materials are crystalline materials and do not absorb moisture easily. The high degree of crystallinity of POM leads to a very high shrinkage, which can be as high as 2% to 3.5%. There are different shrinkage rates for various different reinforced materials.
2).PP Polypropylene
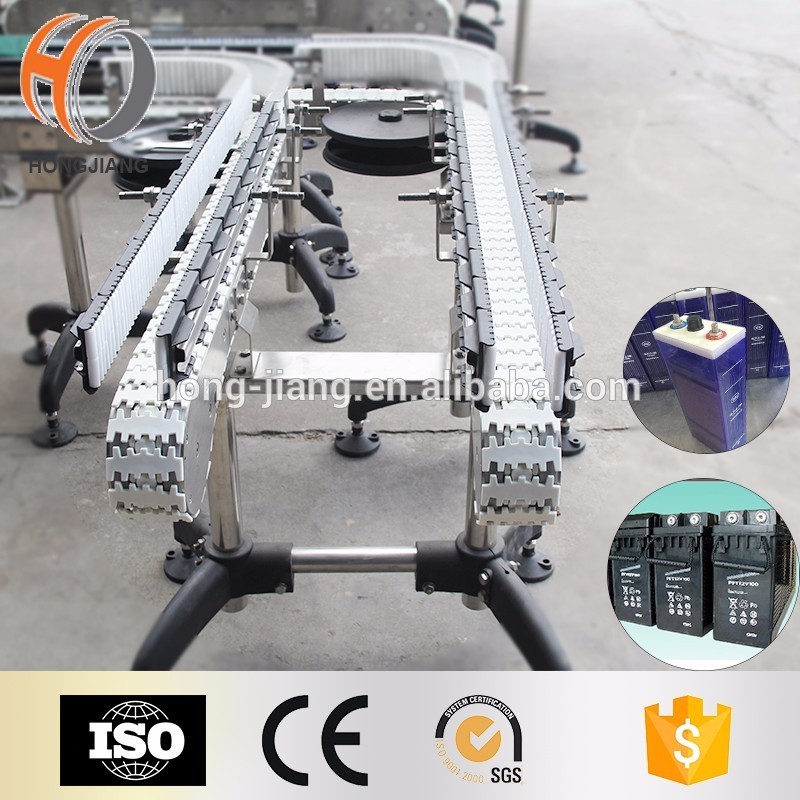
(PP material flexible chain conveyor)
Typical range of applications: automotive industry (mainly use of PP with metal additives: fenders, vents, fans, etc.), instruments (dishwasher door liners, dryer vents, washing machine frames and covers, refrigerator door liners Etc.), Consumer goods for daily use (lawn and garden equipment such as lawn mowers and sprinklers, etc.).
Injection Molding Process Conditions: Drying: Drying is not required if stored properly. Melting temperature: 220 ~ 275 °C, be careful not to exceed 275 °C. Mold temperature: 40 ~ 80 °C, 50 °C recommended. The degree of crystallization is mainly determined by the mold temperature. Injection pressure: up to 1800 bar. Injection speed: In general, using high-speed injection molding can minimize the internal pressure. If the surface of the product is defective, low-speed injection molding at a higher temperature should be used. Runners and gates: For cold runners, typical runner diameters range from 4 to 7 mm. It is recommended to use round injection ports and runners. All types of gates can be used. Typical gate diameters range from 1 to 1.5 mm, but gates as small as 0.7 mm can also be used. For edge gates, the minimum gate depth should be half the wall thickness; the minimum gate width should be at least twice the wall thickness. PP material can use hot runner system completely.
Chemical and Physical Properties PP is a semi-crystalline material. It is harder and has a higher melting point than PE. Since homopolymer PP is very brittle when the temperature of the PP is above 0° C., many commercial PP materials are random copolymers with 1 to 4% ethylene or higher ethylene content clamped segment copolymers. The copolymer PP material has a low heat distortion temperature (100°C), low transparency, low gloss, and low rigidity, but has a stronger impact strength. The strength of PP increases with the ethylene content. The Vicat softening temperature of PP is 150°C. Due to the high degree of crystallinity, this material has very good surface stiffness and scratch resistance. PP does not have the problem of environmental stress cracking. In general, PP is modified by adding glass fibers, metal additives, or thermoplastic rubber. The flow rate of PP has an MFR range of 1 to 40. PP materials with low MFR have better impact resistance but lower strength. For the same MFR material, the copolymer type has higher strength than the homopolymer type. Due to crystallization, PP shrinkage is quite high, typically 1.8 to 2.5%. And the uniformity of the shrinkage direction is much better than that of materials such as PE-HD. Adding 30% of the glass additive can reduce the shrinkage to 0.7%. Homopolymer and copolymer PP materials have excellent resistance to moisture absorption, acid and alkali corrosion, and resistance to dissolution. However, it is not resistant to aromatic hydrocarbons such as benzene solvents, chlorinated hydrocarbon (carbon tetrachloride) solvents, and the like. PP is not as resistant to oxidation as PE at high temperatures.
PA nylon
(PA material conveyor component side guide connect, star knob)
The mechanical properties of PA, such as tensile strength, change with temperature and moisture absorption, so water is a plasticizer for PA. After adding glass fiber, the tensile strength can be increased by about 2 times, and the temperature resistance capability is also improved. Correspondingly, the wear resistance of PA itself is very high, so it can be operated without lubrication. If you want to get special lubrication effect, you can add sulphide to PA.
Suitable plastic products: various gears, Plastic Injection Moulded Split Sprocket , turbines, racks, cams, bearings, propellers, drive belts
◆PA66 has high fatigue strength and steel property, good heat resistance, low friction coefficient, good wear resistance, but high hygroscopicity and insufficient dimensional stability.
Application: Medium-load, wear-resistant force-transmission parts that operate at temperatures <100-120 degrees without lubrication or with less lubrication.
◆ PA6 fatigue strength steel, heat resistance is lower than nylon 66, but good elasticity, better vibration absorption, noise reduction capability. white
Application: Light load, medium temperature (80-100) No lubrication or less lubrication
◆ PA610 strength. Rigid heat resistance lower than nylon 66, but low moisture absorption, good wear resistance. Khaki
Application: With nylon 6, it is recommended to make the gears that require more precise gears, and the working conditions vary greatly in humidity.
◆ PA1001 strength, rigid heat resistance lower than nylon 66, moisture absorption lower than nylon 610, good molding process, good wear resistance.
Application: Parts that work under conditions of light load, low temperature, high humidity, and no lubrication or less lubrication
◆ MCPA strength, fatigue resistance, heat resistance, rigidity are better than PA6 and PA66, hygroscopicity is lower than PA6 and PA66, good wear resistance, can be polymerized directly in the model, should cast large parts. Application: High load, high service temperature (below 120) without lubrication or less lubrication. milky
POM polyoxymethylene, polyacetal (Saigang)
Tensile Strength, Impact Toughness, Rigidity, Fatigue Strength, High Creep Resistance, Good Dimensional Stability, Low Water Absorption, Low Friction Coefficient, Excellent Friction Resistance, High Rigidity at High Temperatures and Water , Chemical resistance, same performance as PA, but the price is low, resistant to repeated distortion, with outstanding rebound ability. Molding is more difficult than nylon and heating is easy to decompose.
Suitable plastic parts: Can replace most of the non-ferrous metals used in various gears, turbines, racks, cams, bearings, pump impellers, automobiles, meters, machine tools, etc.